The Marshall Mix Design method was originally developed by Bruce Marshall of the Mississippi Highway Department in 1939. The main idea of the Marshall Mix Design method involves the selection of the asphalt binder content with a suitable density which satisfies minimum stability and range of flow values.
Advertisements
The Marshall Mix Design method consists mainly of the following steps:
(i) Determination of physical properties, size and gradation of aggregates.
(ii) Selection of types of asphalt binder.
(iii) Prepare initial samples, each with different asphalt binder content.
For example, three samples are made each at 4.5, 5.0, 5.5, 6.0 and 6.5 percent asphalt by dry weight for a total of 15 samples. There should be at least two samples above and two below the estimated optimum asphalt content.
(iv) Plot the following graphs:
(a) Asphalt binder content vs. density
(b) Asphalt binder content vs. Marshall stability
(c) Asphalt binder content vs. flow
(d) Asphalt binder content vs. air voids
(e) Asphalt binder content vs. voids in mineral aggregates
(f) Asphalt binder content vs voids filled with asphalt
(v) Determine the asphalt binder content which corresponds to the air void content of 4 percent
(vi) Determine properties at this optimum asphalt binder content by reference with the graphs. Compare each of these values against design requirements and if all comply with design requirements, then the selected optimum asphalt binder content is acceptable. Otherwise, the mixture should be redesigned.
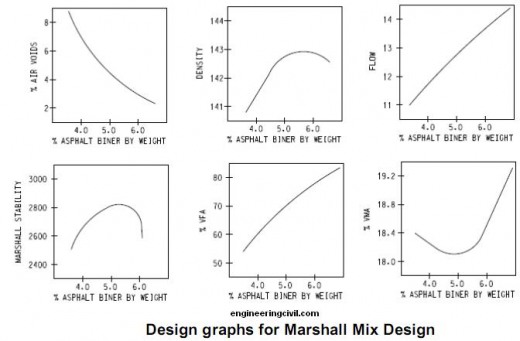
Advertisements
This question is taken from book named – A Self Learning Manual – Mastering Different Fields of Civil Engineering Works (VC-Q-A-Method) by Vincent T. H. CHU.