What is Top-Down Construction?
In top-down construction, permanent structures are built from the ground up, beginning with a deep basement excavation. This method is the inverse of the more common bottom-up approach. This method involves constructing the basement levels in layers as the excavation continues. The concrete floors in basements act as lateral bracing for the surrounding walls. Slabs for the ground floor and basement are poured into the excavation holes. Since all subsequent below-grade levels have been completed, the floors can now act as lateral bracing for the perimeter walls.
Diaphragm walls, or “D” walls as they are more commonly known, are a type of perimeter wall that provides a foolproof answer to any problem that may arise during underground building. D walls are ideal for controlling groundwater movement and maintaining stable earth retention.
Because of its capacity to support the building’s superstructure can be used even before the substructure is finished, speeding up construction. The top-down approach is useful for large-scale, deep-digging projects like building a metro system, a tunnel, or an underground parking garage. It could be the solution in cases when it is desirable to limit soil movement, but no tieback installation is available.
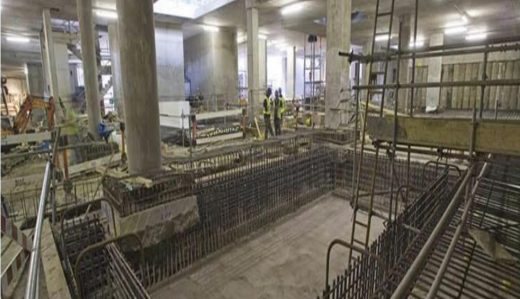
Fig: Top-Down Construction
Courtesy: onlinecivilforum.com
Importance of Top-Down Construction:
- The space between two adjacent boundary walls and the distance between the existing structure and the proposed new construction is inadequate. More than 6 meters have been dug down so far. There is a greater risk of soil collapse during excavation.
- The water level is too high. A Diaphragm Wall or a Continuous Pile could be used instead when a conventional Retaining Wall would be too challenging to cast.
- Greater ground level and basement usage are possible with Top-Down Building. Appropriate for use as a basement by two or more people.
- In this spot, the initial slab of the foundation will serve as a strut. Panels on the retaining wall will prevent soil from sliding down.
The Procedure of Top-Down Construction:
- Getting ready to line up the pile’s cast-in-place bore.
- Bore cast of in situ piles to be cast, and dowels bar to be kept for retaining wall panels. The middle of the piles and the middle of the wall panels should be in the same place. The distance between two piles, from center to center, should be 3.33 meters (suitable for the c/c distance of columns). The piles should have a diameter of 600 mm. Structure consultants will figure out the depth of the piles.
- An excavation set of touching piles can be used as a retaining wall.
- If the basement’s area is bigger and its span is smaller. Then, you can use a diaphragm wall as a retaining wall.
- There will be about a 2-meter-deep dig, and The panels for the retaining wall will be cast in stages, with dowel bars between the piles and dowel bars for the next panel to be kept. If the soil between the piles falls apart, soil nails and wire mesh should be kept on the earth’s side to hold the soil in place. Wall panels will be cast with dowels up to the bottom of the first base slab.
- The soil needs to be shaped and pressed down for the PCC bed before the first base slab can be cast. 50 mm PCC (M15 Grade) needs to be done, and the top layers of PCC must keep the bottom slab level. For the excavation of beams to be done in the same direction. Measurements and PCC or brickwork are done according to the dimensions of the beam on the vertical face.
- After the PCC, 3 mm ply will be laid on top of the PCC. The PCC surface will be separated from the concrete slab surface by nailing a PVC sheet.
- Reinforcing needs to be done according to the plans, and dowel bars from Cast in Situ Piles will be used for beams. For Bottom Up Construction, keep the dowel bars for the slabs next to each other.
- It will be finished with the slab and beam.
- After 14 days of pouring concrete, the PCC below the slab will need to be broken or removed. The excavation will continue, and the retaining wall panels will be set up until the final level of excavation.
- Waterproofing needs to be done, and dowels from Cast in Situ Piles will be used to cast the base slab.
- If needed, the columns will be wrapped in a jacket.
Advantages of Top-Down Construction:
- Basements allow ground-level foundations. The piling rig does not need to be demobilized between basement wall construction and foundation building if piles are offered as the foundation solution. The piling equipment doesn’t need to be craned into the basement hole or pushed down long temporary soil ramps.
- When the basement excavation is covered, rain and other moisture are less of a hindrance to the construction crew working below ground, which is especially helpful in wetter regions and seasons.
- In terms of public safety, a basement built from the top down is preferable. Before beginning the basement excavation, the completed ground floor slab acts as a protection lid preventing unauthorized entry.
- One major advantage of top-down building for basements is its time savings, given that the soil conditions, building heights, and building geometries are all suitable.
- Dust and noise from digging can be muffled by closing the basement entrance.
Disadvantages of Top-Down Construction:
- Due to the plant’s size limitations and restricted access, the excavation operations and substructure construction take longer and cost more.
- Permanent slabs need to be supported vertically in the temporary condition.
- For excavation, holes may need to be left in the slabs.
- More weight is concentrated in the final structure due to its stiffer development during the transitional stages.
- There is no way to build exterior waterproofing.
Conclusion:
In top-down construction, the permanent structure is built reverse, from the surface up, beginning with the basement and proceeding downward through extensive underground excavations. The basement floors are built while the excavation is still in progress. Top-Down construction has sped up project delivery to the client, lowered capital costs dramatically, and improved the quality of the build’s finish. It has also made better use of resources, lowered costs, and cut pollution.
References:
1. Britto, Thomas. “Top Down Construction.” Online Civil Forum, 21 Oct. 2016, www.onlinecivilforum.com/site/top-down-construction.
2. Phan, Thanh Nguyen. “(PDF) Top Down Construction Sequence | Thanh Nguyen Phan – Academia.edu.” (PDF) Top Down Construction Sequence | Thanh Nguyen Phan – Academia.edu, www.academia.edu/38957152/Top_Down_Construction_Sequence. Accessed 14 Oct. 2022.
3. “Top Down Construction Advantages | Top Down Construction Method.” Top Down Construction Advantages | Top down Construction Method, www.constructioncost.co/details-of-top-down-construction-method.html. Accessed 14 Oct. 2022.
4. Tomiša, Adriana. “Top-down Construction Method – Descriptions and Construction Sequence.” Geotech, 23 Jan. 2020, www.geotech.hr/en/top-down-construction-method.
6. Suckling, Quentin, and View more posts. “WHAT IS TOP DOWN CONSTRUCTION AND WHAT ARE ITS BENEFITS – Sheer Force Engineering.” Sheer Force Engineering, 26 Sept. 2021, sheerforceeng.com/what-is-top-down-construction.
Kanwarjot Singh is the founder of Civil Engineering Portal, a leading civil engineering website which has been awarded as the best online publication by CIDC. He did his BE civil from Thapar University, Patiala and has been working on this website with his team of Civil Engineers.
If you have a query, you can ask a question here.